En los últimos años, gracias al rápido desarrollo de la industria de las nuevas energías, la soldadura láser ha penetrado rápidamente en toda la industria de las nuevas energías debido a sus ventajas rápidas y estables. Entre ellos, los equipos de soldadura láser representan la mayor proporción de aplicaciones en toda la industria de las nuevas energías.
Soldadura láserSe ha convertido rápidamente en la primera opción en todos los ámbitos de la vida debido a su rápida velocidad, gran profundidad y pequeña deformación. Desde soldaduras por puntos hasta soldaduras a tope, soldaduras de refuerzo y sellado,soldadura láserProporciona precisión y control incomparables. Desempeña un papel importante en la producción y fabricación industrial, incluida la industria militar, la atención médica, la aeroespacial, las autopartes 3C, la chapa mecánica, las nuevas energías y otras industrias.
En comparación con otras tecnologías de soldadura, la soldadura láser tiene sus ventajas y desventajas únicas.
Ventaja:
1. Velocidad rápida, gran profundidad y pequeña deformación.
2. La soldadura se puede realizar a temperatura normal o en condiciones especiales, y el equipo de soldadura es sencillo. Por ejemplo, un rayo láser no se desplaza en un campo electromagnético. Los láseres pueden soldar en ambientes de vacío, aire o ciertos gases, y pueden soldar materiales que son a través de vidrio o transparentes al rayo láser.
3. Puede soldar materiales refractarios como titanio y cuarzo, y también puede soldar materiales diferentes con buenos resultados.
4. Una vez enfocado el láser, la densidad de potencia es alta. La relación de aspecto puede alcanzar 5:1 y puede alcanzar hasta 10:1 cuando se sueldan dispositivos de alta potencia.
5. Se puede realizar microsoldadura. Una vez enfocado el rayo láser, se puede obtener un pequeño punto que se puede colocar con precisión. Se puede aplicar al ensamblaje y soldadura de micro y pequeñas piezas de trabajo para lograr una producción en masa automatizada.
6. Puede soldar áreas de difícil acceso y realizar soldaduras a larga distancia sin contacto, con gran flexibilidad. Especialmente en los últimos años, la tecnología de procesamiento láser YAG ha adoptado la tecnología de transmisión de fibra óptica, lo que ha permitido que la tecnología de soldadura láser se promueva y aplique más ampliamente.
7. El rayo láser es fácil de dividir en tiempo y espacio, y se pueden procesar múltiples rayos en múltiples ubicaciones simultáneamente, brindando las condiciones para una soldadura más precisa.
Defecto:
1. Se requiere que la precisión del ensamblaje de la pieza de trabajo sea alta y que la posición de la viga en la pieza de trabajo no pueda desviarse significativamente. Esto se debe a que el tamaño del punto del láser después del enfoque es pequeño y la costura de soldadura es estrecha, lo que dificulta la adición de materiales metálicos de aportación. Si la precisión del ensamblaje de la pieza de trabajo o la precisión de posicionamiento de la viga no cumple con los requisitos, es probable que se produzcan defectos de soldadura.
2. El costo de los láseres y los sistemas relacionados es alto y la inversión única es grande.
Defectos comunes de la soldadura láseren la fabricación de baterías de litio
1. Porosidad de soldadura
Defectos comunes ensoldadura láserson los poros. El baño fundido de soldadura es profundo y estrecho. Durante el proceso de soldadura láser, el nitrógeno invade el baño fundido desde el exterior. Durante el proceso de enfriamiento y solidificación del metal, la solubilidad del nitrógeno disminuye con la disminución de la temperatura. Cuando el metal fundido del charco se enfría para comenzar a cristalizar, la solubilidad disminuirá brusca y repentinamente. En este momento, una gran cantidad de gas precipitará formando burbujas. Si la velocidad de flotación de las burbujas es menor que la velocidad de cristalización del metal, se generarán poros.
En aplicaciones en la industria de baterías de litio, a menudo encontramos que es particularmente probable que se formen poros durante la soldadura del electrodo positivo, pero rara vez ocurren durante la soldadura del electrodo negativo. Esto se debe a que el electrodo positivo está hecho de aluminio y el electrodo negativo está hecho de cobre. Durante la soldadura, el aluminio líquido en la superficie se condensa antes de que el gas interno se desborde por completo, evitando que el gas se desborde y forme agujeros grandes y pequeños. Estomas pequeños.
Además de las causas de los poros mencionadas anteriormente, los poros también incluyen el aire exterior, la humedad, el aceite de la superficie, etc. Además, la dirección y el ángulo del soplado de nitrógeno también afectarán la formación de los poros.
¿En cuanto a cómo reducir la aparición de poros de soldadura?
Primero, antessoldadura, las manchas de aceite y las impurezas en la superficie de los materiales entrantes deben limpiarse a tiempo; En la producción de baterías de litio, la inspección del material entrante es un proceso esencial.
En segundo lugar, el flujo de gas protector debe ajustarse de acuerdo con factores como la velocidad de soldadura, la potencia, la posición, etc., y no debe ser ni demasiado grande ni demasiado pequeño. La presión de la capa protectora debe ajustarse según factores como la potencia del láser y la posición del enfoque, y no debe ser ni demasiado alta ni demasiado baja. La forma de la boquilla de la capa protectora debe ajustarse de acuerdo con la forma, dirección y otros factores de la soldadura para que la capa protectora pueda cubrir uniformemente el área de soldadura.
En tercer lugar, controlar la temperatura, la humedad y el polvo del aire en el taller. La temperatura y la humedad ambiente afectarán el contenido de humedad en la superficie del sustrato y el gas protector, lo que a su vez afectará la generación y el escape de vapor de agua en el charco fundido. Si la temperatura y la humedad ambiente son demasiado altas, habrá demasiada humedad en la superficie del sustrato y en el gas protector, generando una gran cantidad de vapor de agua y formando poros. Si la temperatura y la humedad ambiente son demasiado bajas, habrá muy poca humedad en la superficie del sustrato y en el gas protector, lo que reducirá la generación de vapor de agua y reducirá así los poros; Deje que el personal de calidad detecte el valor objetivo de temperatura, humedad y polvo en la estación de soldadura.
Cuarto, el método de oscilación del haz se utiliza para reducir o eliminar los poros en la soldadura láser de penetración profunda. Debido a la adición de oscilación durante la soldadura, la oscilación alternativa de la viga hacia la costura de soldadura provoca la refundición repetida de parte de la costura de soldadura, lo que prolonga el tiempo de residencia del metal líquido en el baño de soldadura. Al mismo tiempo, la desviación del haz también aumenta el aporte de calor por unidad de superficie. Se reduce la relación profundidad-ancho de la soldadura, lo que favorece la aparición de burbujas, eliminando así los poros. Por otro lado, la oscilación de la viga hace que el pequeño orificio oscile en consecuencia, lo que también puede proporcionar una fuerza de agitación para el baño de soldadura, aumentar la convección y agitación del baño de soldadura y tener un efecto beneficioso en la eliminación de los poros.
Quinto, la frecuencia del pulso, la frecuencia del pulso se refiere al número de pulsos emitidos por el rayo láser por unidad de tiempo, lo que afectará la entrada de calor y la acumulación de calor en el baño fundido, y luego afectará el campo de temperatura y el campo de flujo en el baño fundido. piscina. Si la frecuencia del pulso es demasiado alta, provocará una entrada excesiva de calor en el baño fundido, lo que hará que la temperatura del baño fundido sea demasiado alta, lo que producirá vapor metálico u otros elementos que son volátiles a altas temperaturas, lo que resulta en poros. Si la frecuencia del pulso es demasiado baja, provocará una acumulación insuficiente de calor en el baño fundido, lo que provocará que la temperatura del baño fundido sea demasiado baja, lo que reducirá la disolución y el escape del gas, lo que provocará poros. En términos generales, la frecuencia del pulso debe elegirse dentro de un rango razonable según el espesor del sustrato y la potencia del láser, y evitar que sea demasiado alta o demasiado baja.
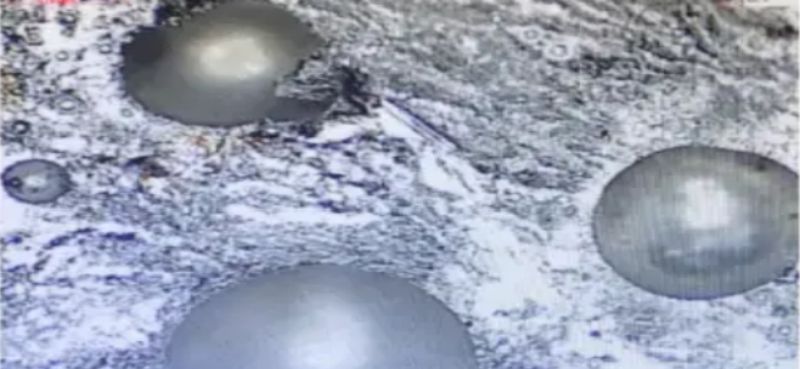
Orificios de soldadura (soldadura por láser)
2. Salpicaduras de soldadura
Las salpicaduras generadas durante el proceso de soldadura, la soldadura láser, afectarán gravemente la calidad de la superficie de la soldadura y contaminarán y dañarán la lente. El rendimiento general es el siguiente: una vez completada la soldadura láser, aparecen muchas partículas metálicas en la superficie del material o pieza de trabajo y se adhieren a la superficie del material o pieza de trabajo. El rendimiento más intuitivo es que al soldar en el modo del galvanómetro, después de un período de uso de la lente protectora del galvanómetro, habrá picaduras densas en la superficie, y estas picaduras son causadas por salpicaduras de soldadura. Después de mucho tiempo, es fácil bloquear la luz y habrá problemas con la luz de soldadura, lo que resultará en una serie de problemas como soldadura rota y soldadura virtual.
¿Cuáles son las causas de las salpicaduras?
En primer lugar, la densidad de potencia: cuanto mayor es la densidad de potencia, más fácil es generar salpicaduras, y las salpicaduras están directamente relacionadas con la densidad de potencia. Este es un problema que tiene un siglo de antigüedad. Al menos hasta ahora, la industria no ha podido solucionar el problema de las salpicaduras y sólo puede decir que se ha reducido ligeramente. En la industria de las baterías de litio, las salpicaduras son el mayor culpable del cortocircuito de la batería, pero no han podido resolver la causa raíz. El impacto de las salpicaduras en la batería sólo puede reducirse desde el punto de vista de la protección. Por ejemplo, se agrega un círculo de puertos de eliminación de polvo y cubiertas protectoras alrededor de la parte de soldadura, y se agregan filas de cuchillas de aire en círculos para evitar el impacto de salpicaduras o incluso daños a la batería. Se puede decir que la destrucción del medio ambiente, los productos y los componentes alrededor de la estación de soldadura ha agotado los medios.
En cuanto a resolver el problema de las salpicaduras, sólo se puede decir que reducir la energía de soldadura ayuda a reducir las salpicaduras. Reducir la velocidad de soldadura también puede ayudar si la penetración es insuficiente. Pero en algunos requisitos de procesos especiales, tiene poco efecto. Es el mismo proceso, diferentes máquinas y diferentes lotes de materiales tienen efectos de soldadura completamente diferentes. Por lo tanto, existe una regla no escrita en la nueva industria energética: un conjunto de parámetros de soldadura para un equipo.
En segundo lugar, si no se limpia la superficie del material procesado o de la pieza de trabajo, las manchas de aceite o los contaminantes también provocarán graves salpicaduras. En este momento, lo más sencillo es limpiar la superficie del material procesado.
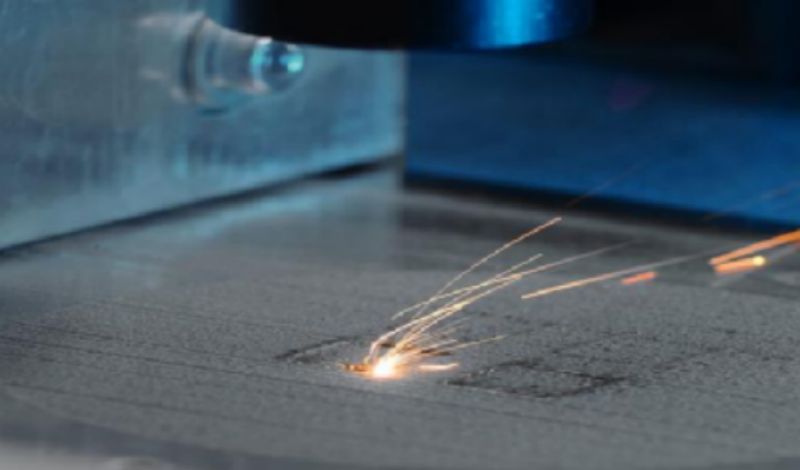
3. Alta reflectividad de la soldadura láser.
En términos generales, la alta reflexión se refiere al hecho de que el material de procesamiento tiene una resistividad pequeña, una superficie relativamente lisa y una tasa de absorción baja para los láseres de infrarrojo cercano, lo que conduce a una gran cantidad de emisión de láser, y porque la mayoría de los láseres se utilizan. en vertical Debido al material o a una pequeña cantidad de inclinación, la luz láser que regresa vuelve a entrar en el cabezal de salida, e incluso parte de la luz que regresa se acopla a la fibra transmisora de energía y se transmite de regreso a lo largo de la fibra hacia el interior. del láser, haciendo que los componentes centrales dentro del láser continúen a alta temperatura.
Cuando la reflectividad es demasiado alta durante la soldadura láser, se pueden tomar las siguientes soluciones:
3.1 Utilice un revestimiento antirreflectante o trate la superficie del material: recubrir la superficie del material de soldadura con un revestimiento antirreflectante puede reducir eficazmente la reflectividad del láser. Este recubrimiento suele ser un material óptico especial con baja reflectividad que absorbe la energía del láser en lugar de reflejarla. En algunos procesos, como la soldadura de colectores de corriente, la conexión blanda, etc., la superficie también se puede estampar.
3.2 Ajuste el ángulo de soldadura: Al ajustar el ángulo de soldadura, el rayo láser puede incidir sobre el material de soldadura en un ángulo más apropiado y reducir la aparición de reflejos. Normalmente, hacer que el rayo láser incida perpendicularmente a la superficie del material a soldar es una buena forma de reducir los reflejos.
3.3 Adición de absorbente auxiliar: Durante el proceso de soldadura, se agrega a la soldadura una cierta cantidad de absorbente auxiliar, como polvo o líquido. Estos absorbentes absorben la energía del láser y reducen la reflectividad. Es necesario seleccionar el absorbente adecuado en función de los materiales de soldadura específicos y los escenarios de aplicación. En la industria de las baterías de litio, esto es poco probable.
3.4 Utilice fibra óptica para transmitir el láser: Si es posible, se puede utilizar fibra óptica para transmitir el láser a la posición de soldadura para reducir la reflectividad. Las fibras ópticas pueden guiar el rayo láser al área de soldadura para evitar la exposición directa a la superficie del material de soldadura y reducir la aparición de reflejos.
3.5 Ajuste de los parámetros del láser: Al ajustar parámetros como la potencia del láser, la distancia focal y el diámetro focal, se puede controlar la distribución de la energía del láser y reducir los reflejos. Para algunos materiales reflectantes, reducir la potencia del láser puede ser una forma eficaz de reducir los reflejos.
3.6 Utilice un divisor de haz: un divisor de haz puede guiar parte de la energía del láser hacia el dispositivo de absorción, reduciendo así la aparición de reflejos. Los dispositivos de división del haz normalmente constan de componentes ópticos y absorbentes, y seleccionando los componentes apropiados y ajustando el diseño del dispositivo, se puede lograr una menor reflectividad.
4. Soldadura socavada
En el proceso de fabricación de baterías de litio, ¿qué procesos tienen más probabilidades de provocar una subcotización? ¿Por qué se produce la subcotización? Analicémoslo.
Socavado, generalmente las materias primas de soldadura no están bien combinadas entre sí, el espacio es demasiado grande o aparece la ranura, la profundidad y el ancho son básicamente mayores a 0,5 mm, la longitud total es mayor al 10% de la longitud de la soldadura, o mayor que el estándar de proceso del producto la longitud solicitada.
En todo el proceso de fabricación de baterías de litio, es más probable que se produzca socavación, y generalmente se distribuye en la soldadura previa y soldadura de sellado de la placa de cubierta cilíndrica y la soldadura previa y soldadura de sellado de la placa de cubierta de carcasa de aluminio cuadrada. La razón principal es que la placa de cubierta de sellado necesita cooperar con la carcasa para soldar, el proceso de coincidencia entre la placa de cubierta de sellado y la carcasa es propenso a espacios de soldadura excesivos, ranuras, colapso, etc., por lo que es particularmente propenso a socavaduras. .
Entonces, ¿qué causa la subcotización?
Si la velocidad de soldadura es demasiado rápida, el metal líquido detrás del pequeño orificio que apunta al centro de la soldadura no tendrá tiempo de redistribuirse, lo que provocará solidificación y socavados en ambos lados de la soldadura. En vista de la situación anterior, necesitamos optimizar los parámetros de soldadura. En pocas palabras, se repiten experimentos para verificar varios parámetros y se continúa haciendo DOE hasta que se encuentran los parámetros apropiados.
2. Los espacios de soldadura excesivos, ranuras, colapsos, etc. de los materiales de soldadura reducirán la cantidad de metal fundido que llena los espacios, lo que aumenta la probabilidad de que se produzcan socavaduras. Se trata de una cuestión de equipamiento y de materias primas. Si las materias primas de soldadura cumplen con los requisitos de material entrante de nuestro proceso, si la precisión del equipo cumple con los requisitos, etc. La práctica normal es torturar y golpear constantemente a los proveedores y a las personas a cargo del equipo.
3. Si la energía cae demasiado rápido al final de la soldadura láser, el pequeño orificio puede colapsar, lo que resulta en una socavación local. La combinación correcta de potencia y velocidad puede prevenir eficazmente la formación de socavaduras. Como dice el viejo refrán, repita los experimentos, verifique varios parámetros y continúe DOE hasta que encuentre los parámetros correctos.
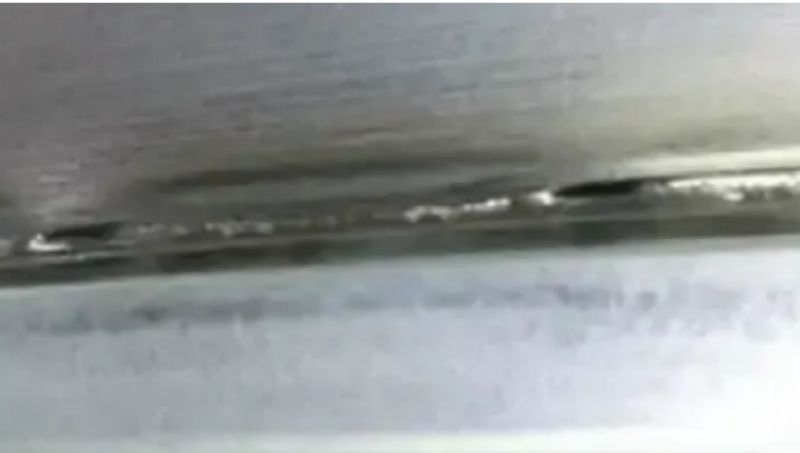
5. Colapso del centro de soldadura
Si la velocidad de soldadura es lenta, el baño fundido será más grande y ancho, aumentando la cantidad de metal fundido. Esto puede dificultar el mantenimiento de la tensión superficial. Cuando el metal fundido se vuelve demasiado pesado, el centro de la soldadura puede hundirse y formar hundimientos y picaduras. En este caso, es necesario reducir adecuadamente la densidad de energía para evitar el colapso del charco de fusión.
En otra situación, el espacio de soldadura simplemente forma un colapso sin provocar perforación. Sin duda se trata de un problema de ajuste a presión del equipo.
Una comprensión adecuada de los defectos que pueden ocurrir durante la soldadura láser y las causas de los diferentes defectos permite un enfoque más específico para resolver cualquier problema anormal de soldadura.
6. Grietas en la soldadura
Las grietas que aparecen durante la soldadura láser continua son principalmente grietas térmicas, como grietas cristalinas y grietas por licuefacción. La principal causa de estas grietas son las grandes fuerzas de contracción que genera la soldadura antes de que solidifique por completo.
También existen las siguientes razones para las grietas en la soldadura láser:
1. Diseño de soldadura irrazonable: el diseño inadecuado de la geometría y el tamaño de la soldadura puede provocar la concentración de la tensión de soldadura y provocar grietas. La solución es optimizar el diseño de la soldadura para evitar la concentración de tensiones de soldadura. Puede utilizar soldaduras compensadas adecuadas, cambiar la forma de la soldadura, etc.
2. Falta de coincidencia de los parámetros de soldadura: la selección inadecuada de los parámetros de soldadura, como una velocidad de soldadura demasiado rápida, una potencia demasiado alta, etc., puede provocar cambios de temperatura desiguales en el área de soldadura, lo que resulta en grandes tensiones de soldadura y grietas. La solución es ajustar los parámetros de soldadura para que coincidan con el material específico y las condiciones de soldadura.
3. Mala preparación de la superficie de soldadura: No limpiar y tratar adecuadamente la superficie de soldadura antes de soldar, como eliminar óxidos, grasa, etc., afectará la calidad y resistencia de la soldadura y fácilmente provocará grietas. La solución es limpiar y pretratar adecuadamente la superficie de soldadura para garantizar que las impurezas y contaminantes en el área de soldadura sean tratados de manera efectiva.
4. Control inadecuado del aporte de calor de soldadura: un control deficiente del aporte de calor durante la soldadura, como una temperatura excesiva durante la soldadura, una velocidad de enfriamiento inadecuada de la capa de soldadura, etc., provocará cambios en la estructura del área de soldadura, lo que provocará grietas. . La solución es controlar la temperatura y la velocidad de enfriamiento durante la soldadura para evitar el sobrecalentamiento y el enfriamiento rápido.
5. Alivio de tensión insuficiente: un tratamiento de alivio de tensión insuficiente después de la soldadura dará como resultado un alivio de tensión insuficiente en el área soldada, lo que fácilmente provocará grietas. La solución es realizar un tratamiento adecuado de alivio de tensiones después de la soldadura, como un tratamiento térmico o un tratamiento por vibración (motivo principal).
En cuanto al proceso de fabricación de las baterías de litio, ¿qué procesos tienen más probabilidades de provocar grietas?
Generalmente, es probable que se produzcan grietas durante la soldadura de sellado, como la soldadura de sellado de carcasas de acero cilíndricas o carcasas de aluminio, la soldadura de sellado de carcasas de aluminio cuadradas, etc. Además, durante el proceso de empaquetado del módulo, la soldadura del colector de corriente también es propensa. a las grietas.
Por supuesto, también podemos utilizar alambre de aportación, precalentamiento u otros métodos para reducir o eliminar estas grietas.
Hora de publicación: 01-sep-2023